Complete Guide to Cardan Shaft Selection for Heavy Industrial Machinery in India 2025
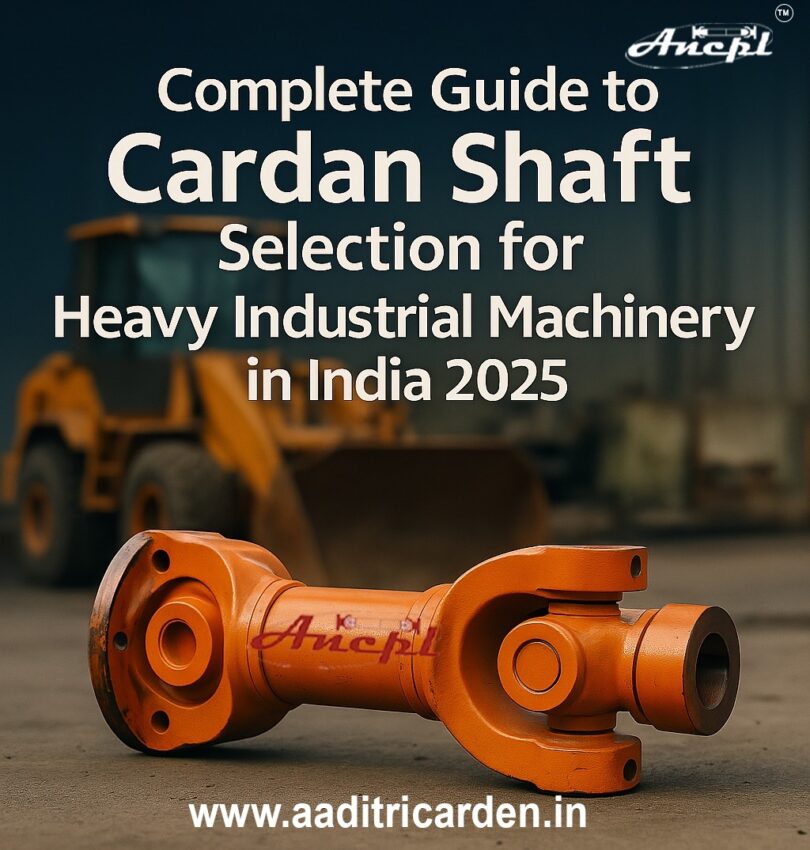
Introduction: The Critical Choice for Industrial Might
Ever wondered what keeps the colossal machines in India’s bustling mines, busy construction sites, and thriving manufacturing plants running smoothly, often under immense strain? Chances are, a robust cardan shaft is quietly doing its job, transmitting power with remarkable efficiency. As we charge into 2025, the stakes are higher than ever. With India’s industrial sector scaling new heights, making the right cardan shaft selection for heavy industrial machinery in India 2025 isn’t just about functionality; it’s about optimizing uptime, reducing costly breakdowns, and ensuring long-term operational excellence.
This isn’t just another technical manual. This guide is crafted to empower you with practical insights, drawing from real-world scenarios and industry best practices. We’ll cut through the jargon, helping you confidently choose the ideal cardan shaft that stands up to India’s unique industrial demands.
Unpacking the Cardan Shaft: More Than Just a Rod
Before we dive into selection, let’s briefly understand this vital component.
What Exactly is a Cardan Shaft?
At its core, a cardan shaft (often called a drive shaft or propeller shaft) is a mechanical marvel designed to transmit torque and rotation between components that aren’t perfectly aligned. Imagine a heavy-duty excavator or a massive rolling mill – their engines and driven axles are rarely in a perfectly straight line. This is where the cardan shaft, with its flexible universal joints, steps in, ensuring seamless power flow despite angular misalignments.
The Anatomy of Reliability: Key Components
A typical cardan shaft consists of a few crucial parts:
- Universal Joints (U-Joints): These are the heart of the cardan shaft’s flexibility. They allow the shaft to bend and transmit power at varying angles without binding. You’ll often find two or more U-joints on a single shaft.
- Shaft Tubes: The central, hollow tubes that connect the universal joints and transmit the rotational force. Their material and thickness are paramount for handling torque.
- Splined Connections: These allow the shaft to change length, accommodating movement in the machinery (e.g., suspension travel in off-highway vehicles).
- Flange Yokes: The connecting points that attach the cardan shaft to the machine’s driving and driven components (like gearboxes, differentials, or rolling mill stands).
Why Your Cardan Shaft Selection Matters: The Indian Industrial Context
In heavy industrial settings across India, from the dusty opencast mines of Jharkhand to the sprawling steel plants of Odisha, cardan shafts are subjected to extreme conditions: heavy loads, constant vibrations, abrasive environments, and often, high temperatures.
Ensuring Operational Continuity and Efficiency
A well-chosen cardan shaft minimizes energy loss during power transmission, directly contributing to the overall efficiency of your machinery. Conversely, a poorly chosen or failing shaft can lead to:
- Excessive Vibrations: Causing premature wear on bearings, seals, and other vital components.
- Increased Downtime: Leading to significant production losses.
- Safety Hazards: A catastrophic shaft failure can be dangerous.
- Higher Maintenance Costs: Frequent replacements and repairs drain resources.
This is precisely why astute cardan shaft selection for heavy industrial machinery in India 2025 is non-negotiable for any forward-thinking operation.
Insights into large-scale engineering projects and component manufacturing
Critical Factors for Optimal Cardan Shaft Selection
Choosing the right shaft isn’t a one-size-fits-all situation. It demands a systematic approach.
1. Torque and Speed Requirements:
This is paramount. You need to accurately calculate the maximum torque (power) and rotational speed your machinery will demand from the shaft. Over-specifying can be wasteful, but under-specifying is a recipe for disaster.
- Peak Torque: The highest momentary load the shaft will experience.
- Operating Torque: The continuous load.
- Critical Speed: The rotational speed at which the shaft can resonate, leading to dangerous vibrations. Ensure your operating speed is well below this.
Insider Tip: Don’t just rely on nameplate power. Consider starting torques, shock loads, and transient conditions, especially in heavy-duty applications like stone crushers or steel rolling mills.
2. Operating Angle and Misalignment:
Cardan shafts excel at handling angles. But there are limits. The operating angle (the angle between the driving and driven shafts) impacts the life and performance of the universal joints.
- Dynamic Angles: Occur when the angle changes during operation (e.g., in a vehicle suspension system).
- Static Angles: Fixed angles between connected components.
- Excessive or constantly varying angles can accelerate wear. Work closely with the manufacturer to ensure the shaft’s design can handle your specific angular requirements.
3. Environmental Conditions:
India’s diverse climate and industrial environments pose unique challenges.
- Temperature: Extreme heat (think a steel mill) or cold (high-altitude mining) can affect material properties and lubricant viscosity.
- Dust, Dirt, and Abrasives: Common in construction and mining. Proper sealing and robust materials are crucial.
- Moisture and Corrosion: High humidity, rain, or exposure to chemicals (e.g., in processing plants) demand corrosion-resistant coatings or materials like stainless steel.
- Vibration and Shock Loads: Inherent in heavy machinery. The shaft must be designed to absorb and withstand these forces without fatiguing.
4. Lubrication and Maintenance Ease:
A well-lubricated shaft is a long-lasting shaft. Consider:
- Greasing Intervals: How frequently does it need lubrication?
- Lubricant Type: Does it require specific high-performance grease?
- Accessibility: Are grease nipples easily accessible for routine maintenance?
Opting for shafts with longer maintenance intervals or sealed-for-life universal joints (where applicable) can significantly reduce operational costs and downtime, especially for remote or hard-to-reach machinery.
5. Material Selection and Manufacturing Quality:
This is where the rubber meets the road. The strength and durability of a cardan shaft largely depend on the materials used and the precision of its manufacturing. High-grade alloy steels (like AISI 4140 or EN19) are common for their excellent strength-to-weight ratio and fatigue resistance.
- Forged Components: Often superior to cast components for critical parts like yokes, offering better grain structure and strength.
- Balancing: Precisely balanced shafts reduce vibrations, extending the life of the shaft itself and connected components.
- Strict Quality Control: Look for manufacturers with ISO certifications and rigorous testing protocols.
This detailed consideration ensures your cardan shaft selection for heavy industrial machinery in India 2025 is future-proof.
Leading the Way: Top Cardan Shaft Manufacturers in India
India boasts a robust engineering and manufacturing sector, with several companies producing high-quality cardan shafts. While the market is dynamic, some key players consistently deliver:
- Bharat Heavy Electricals Limited (BHEL): A public sector giant with vast experience in heavy engineering, BHEL produces a wide array of industrial components, including robust cardan shafts for various heavy-duty applications. Their focus on quality and adherence to international standards make them a reliable choice. (Source: BHEL official website)
- Larsen & Toubro (L&T): As a conglomerate deeply rooted in engineering and construction, L&T’s manufacturing prowess extends to specialized industrial components. They are known for their engineering solutions for core sectors, which often include heavy-duty power transmission elements. (Source: L&T official website)
- Local Specialized Manufacturers: Beyond the giants, several reputable Indian companies specialize solely in drive shafts and power transmission solutions, serving specific niches within heavy industry. It’s worth exploring these for tailored solutions and potentially faster lead times.
When considering a supplier, always verify their certifications, customer testimonials, and after-sales support network, particularly important in geographically dispersed Indian industrial hubs.
Case Studies: Real-World Impact of Smart Selection
Let’s look at how thoughtful cardan shaft selection for heavy industrial machinery in India 2025 translates into tangible benefits.
- Scenario 1: The Resilient Rolling Mill: A steel rolling mill in Chhattisgarh faced frequent breakdowns due to premature wear of its cardan shafts, leading to significant production losses. After a detailed analysis of torque peaks and operating angles, they opted for custom-engineered shafts with enhanced alloy steel and optimized universal joints. The result? A 35% reduction in shaft-related downtime within the first year and extended service intervals, proving the value of a tailored solution.
- Scenario 2: The Indestructible Excavator Fleet: An infrastructure development company operating in the rugged terrains of Himachal Pradesh upgraded its excavator fleet. They switched to cardan shafts designed for extreme shock loads and equipped with superior sealing for protection against dust and moisture. This seemingly small change led to a noticeable improvement in vehicle uptime and a significant drop in repair costs for the drive train, underscoring the importance of environmental considerations in shaft design.
The Road Ahead: Future Trends in Cardan Shaft Technology
The world of industrial machinery is constantly evolving, and cardan shafts are no exception. Looking towards 2025 and beyond, expect to see:
- Advanced Materials: Research in lightweight, high-strength composites and advanced steel alloys will lead to more durable and energy-efficient shafts.
- Smart Shafts: Integration of sensors for real-time monitoring of vibration, temperature, and torque. This data, combined with AI and IoT, will enable predictive maintenance, alerting operators to potential issues before failure occurs. Imagine a shaft telling you it needs attention!
- Modularity and Standardization: Increased focus on modular designs and standardization to simplify replacement and reduce inventory costs.
- Sustainability: Manufacturers will increasingly focus on reducing the environmental footprint of production and improving the recyclability of components.
These innovations will make the task of cardan shaft selection for heavy industrial machinery in India 2025 even more sophisticated, but also more rewarding in terms of operational benefits.
Top 5 Cardan Shaft Manufacturers in India: Quality, Cost & Delivery
Conclusion: Your Partner in Power Transmission
The cardan shaft might be an unsung hero, but its role in the reliability and efficiency of heavy industrial machinery is undeniable. Making the right cardan shaft selection for heavy industrial machinery in India 2025 is a strategic investment that pays dividends in reduced downtime, lower maintenance costs, and ultimately, a more productive operation.
By carefully considering factors like torque, operating angles, environmental challenges, and the quality of manufacturing, you can ensure your machinery runs smoothly for years to come. Don’t underestimate the power of informed decisions.
Ready to optimize your machinery’s performance? If you have specific questions about your application or need assistance in navigating the complexities of cardan shaft selection, don’t hesitate to reach out. Share your thoughts or experiences in the comments below – let’s learn from each other and build a stronger, more efficient industrial future for India!
Leave a Reply